Gas cutting metal: oxygen consumption and propane, technology
The most common way to carry out metal cutting today is autogenous, it is also called gas or oxygen. Its essence comes down to the fact that under the influence of gas flame, the metal heats up and begins to melt, and under the influence of the oxygen jet, its combustion occurs, making a narrow groove.
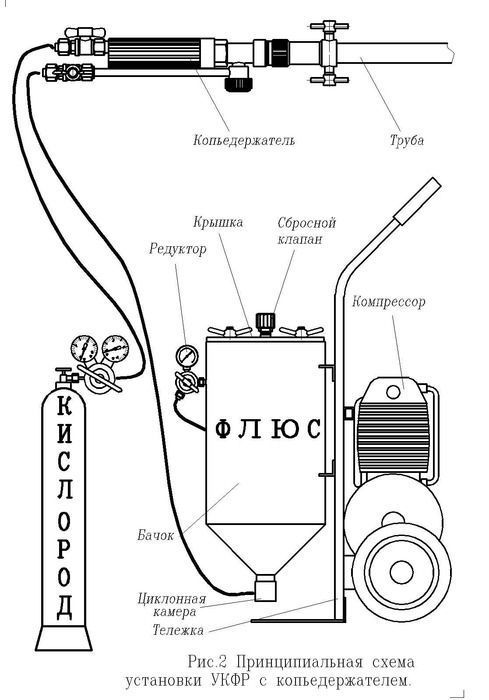
Acetylene, propane-butane, natural, coke gas is used as a heater.
Metal cutting can be classified depending on the desired final result:
- superficial;
- separation;
- cutting spear.
Surface gas cutting applies in cases where it is necessary to remove metal layers to form slots, grooves and other structural elements.
The dividing species provides for the implementation of the end-to-end cut, to obtain the required amount of metal elements, parts. Borrowing metal to obtain deep or through holes is called a sharp spear.
Technological process
In independence from cutting types, the technology of performing this process will be the same. The combustion of gas provides a temperature from 1000 to 1300 ° C, it is enough to melt the solid steel. During this, a strong jet of oxygen is supplied, which reacts with molten metal molecules, oxidizing them.
As a result, the cut is obtained. Oxygen is fed under high pressure, often it reaches 12 atmospheres, such a jet even without feeding the fire can cut the skin.
The structure of the cutting apparatus is designed in this way:
- gas-burner;
- two cylinders;
- mixer;
- pressure regulator;
- hoses.
The gas burner consists of a head with several nozzles, mostly three. Through two side, a fuel substance is fed, through the third, which is located in the middle, oxygen is supplied. Cylinders are intended directly for gas and oxygen, depending on the volumes of the intended work, the corresponding cylinders are selected.
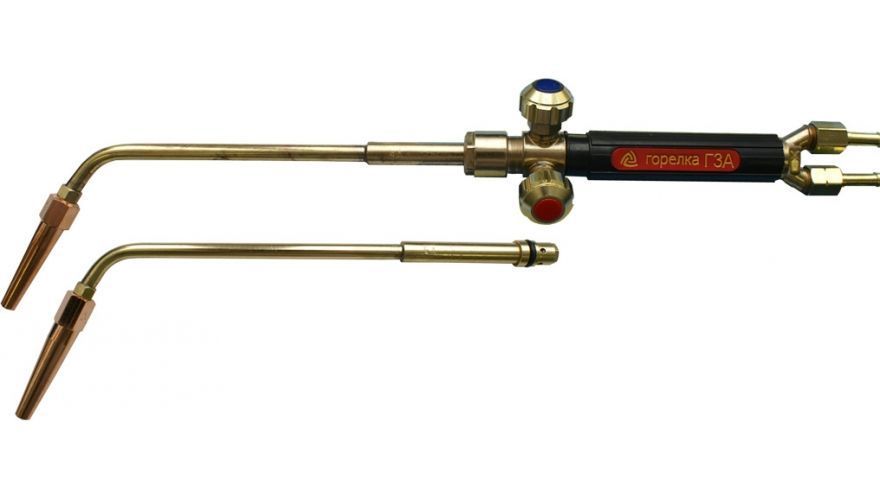
To ensure one hour of continuous operation, an average of 0.7 m 3 acetylene (1 m 3 of propane) and 10 m 3 oxygen will be consumed. In general, the required amount of raw materials will depend on the density of the metal and the required temperature for its heating. Reduced propane consumption can be due to special nozzles on nozzles, which fix the supply of gas in a certain direction, the closer the supply to the oxygen jet, the fuel consumption will increase.
The hoses are necessary for the supply of oxygen and fuel from cylinders into the mixer, they are also called the sleeves. The material from which the hoses are made are two-layer tires, between the layers of the frame, made of a cotton thread. Diameter - up to 12 mm, the possibility of operation at air temperature is not lower than -35 o C.
Pressure regulator is required to provide different modes and cutting speeds. Feeding a smaller amount of fuel can be provided with a low temperature, which is necessary for fine steel or metal of low strength, as well as reduce the consumption of raw materials.
Another important function of the gearbox is to maintain a uniform pressure level. If the gas supply is interrupted during the cutting process, the metal will quickly cool and further processing will become impossible.
Metal cutting with propane and oxygen
Necessary equipment
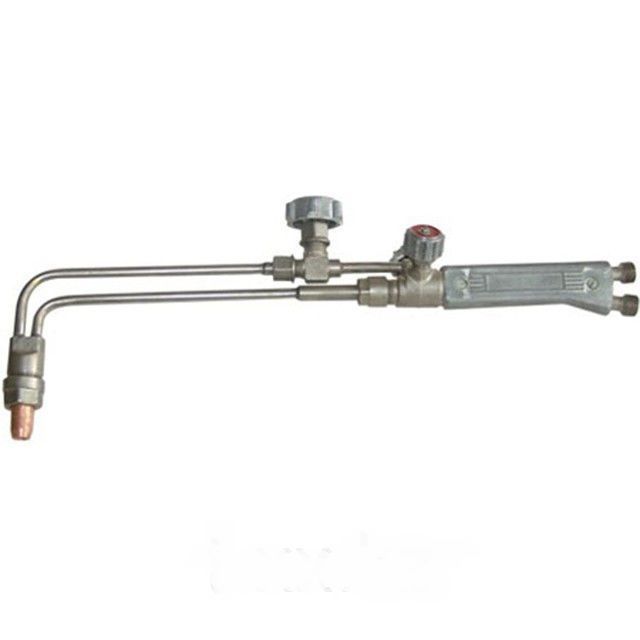
The very first cutter was the R1-01 device, it was constructed in the USSR, then more upgraded models appeared - P2 and P3. The devices are distinguished by the sizes of the nozzles and the power of the gearbox. More modern manual installations:
- Change;
- Quicky;
- Orbit;
- SECATOR.
They are characterized by a set of additional features and performance.
Quicky can carry out curly cutting, according to the specified drawings, the speed of work reaches 1000 mm per minute, the maximum allowable thickness of the metal to 100 mm. The device has a set of removable nozzles to provide metal sheets or pipes of various thickness.
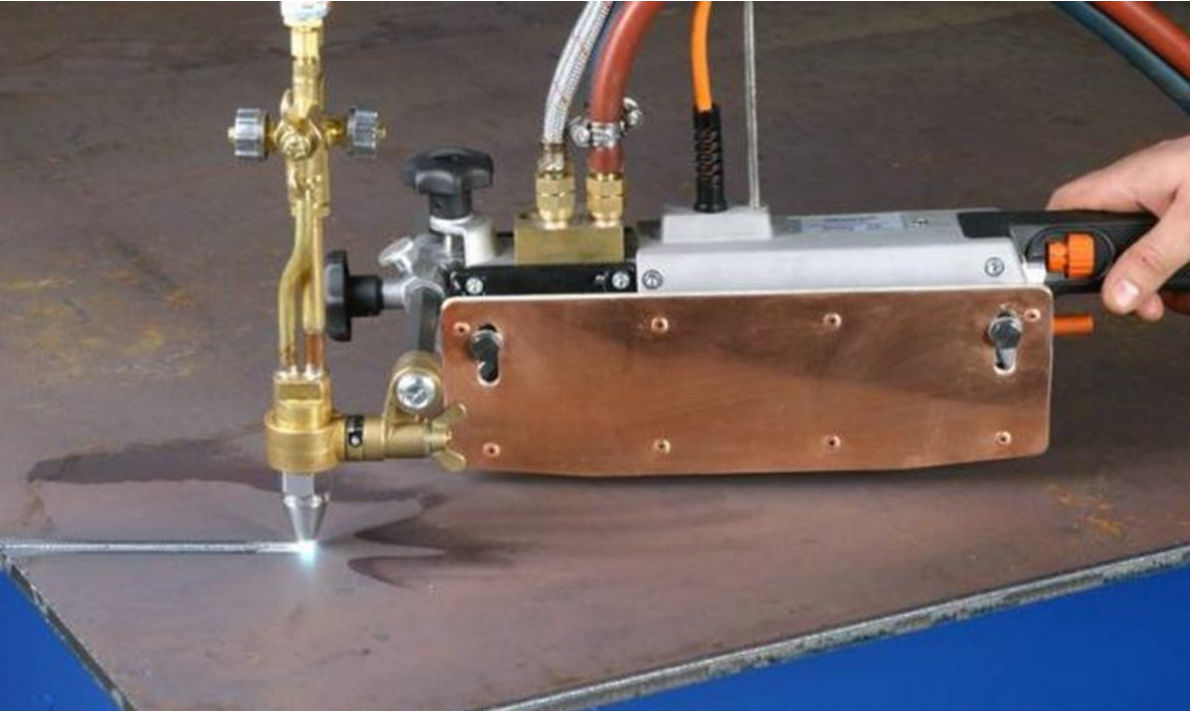
This apparatus can work using various types of combustible gas, in contrast to the prototype P1-01, which works only on acetylene.
A manual secator cutter has more improved characteristics compared to counterparts.
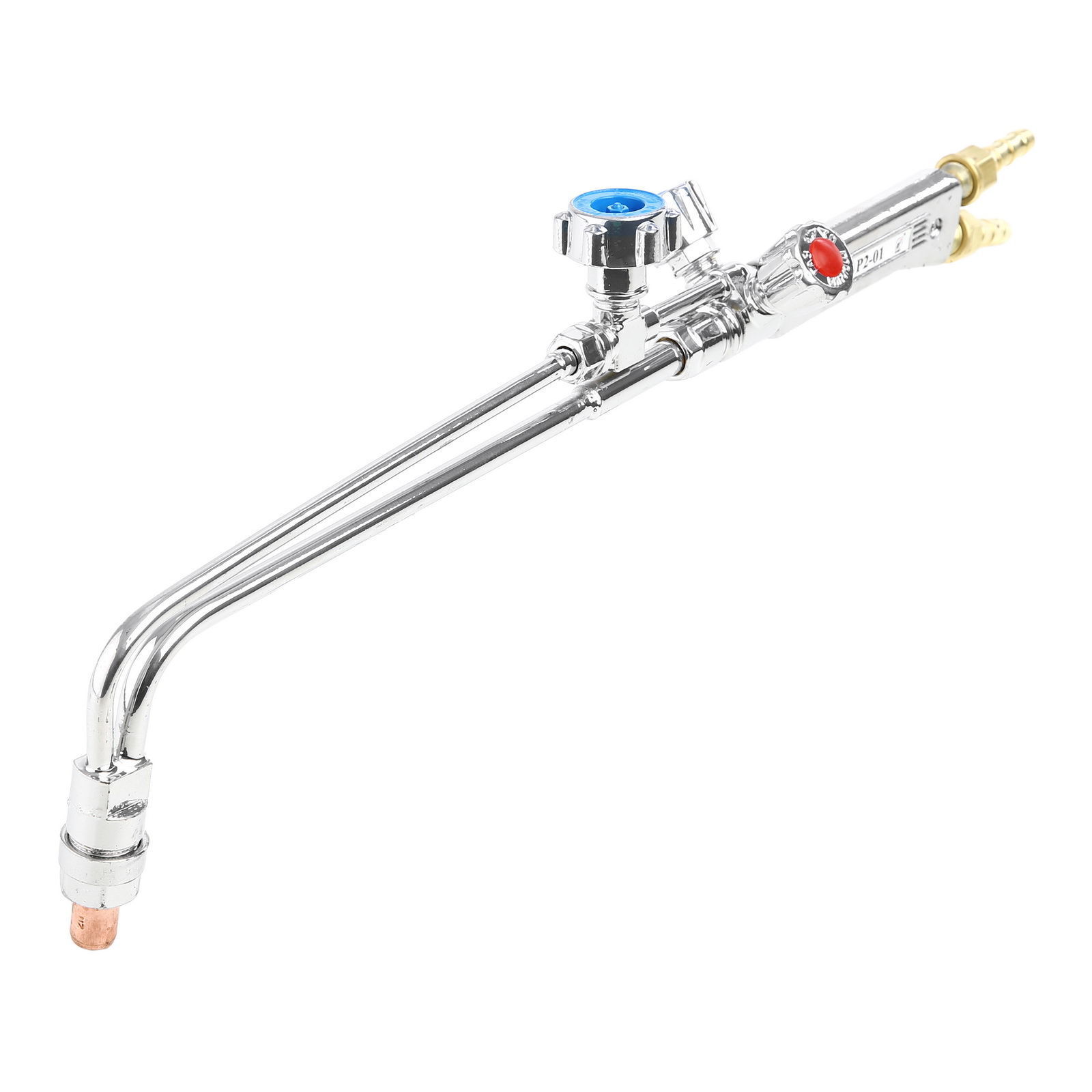
With it, you can handle metal with a thickness of up to 300 mm, these are provided with additional nozzles included in the kit, they are removable and they can be purchased additionally, as wear. Secator can produce the following types of cutting:
- figured;
- straightforward
- ring;
- under the screw.
The speed can be adjusted in the range from 100,1200 mm per minute, and using the built-in sleeve coupling, a smooth movement of a metal sheet is provided. Air-cooled reducer provides cleaner work and reduces the fuel consumption.
The above models belong to manual, that is, they are compact, manage using the hands of the wizard. But for large volumes of the metal, working with such
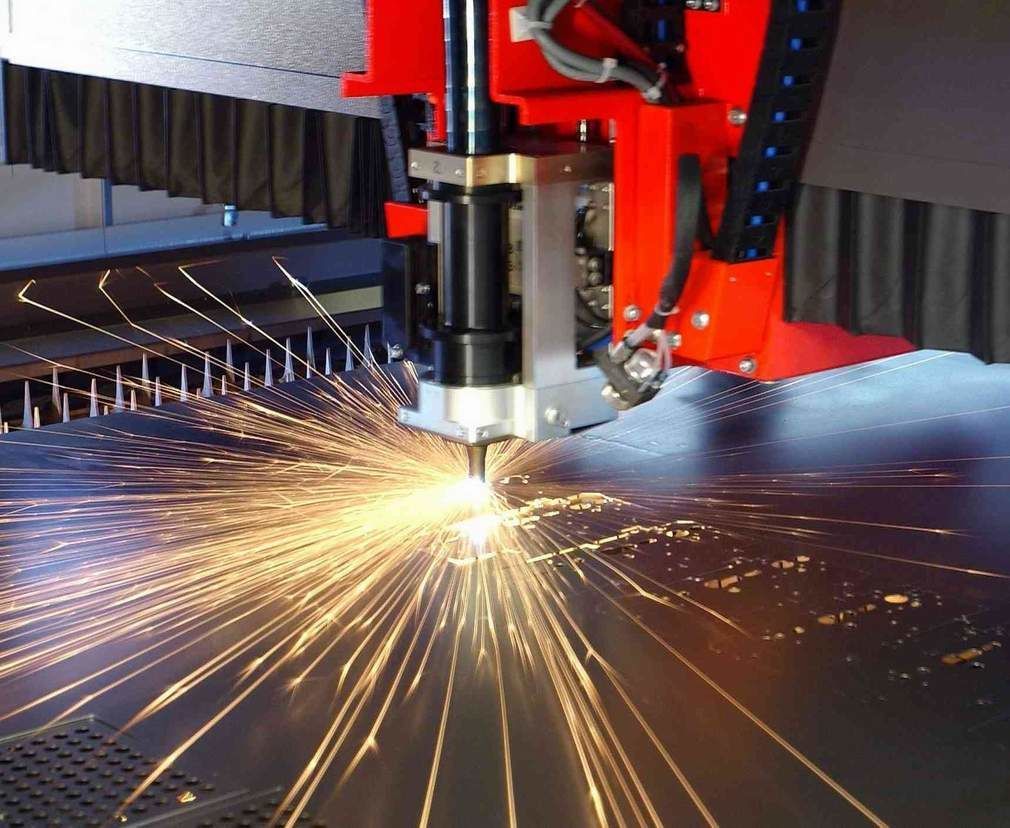
installations are inconvenient and not effectively. For industrial production, stationary cutting installations are applied - this is essentially the same technology.
They are a machine with a tabletop in which the cutting mechanism is built. Its work provides electric
the compressor for which the power grid is needed from at least 380 V and three-phase sockets. The technology of working models of stationary cutting installations is nothing, but differs from manual. The difference is only in performance, maximum heating temperature, and ability to process metal, more than 300 mm thick.
Metal cutting conditions
Gas cutting of metal will be effective only when the metal ignition temperature is less than the melting point. Such proportions are observed in low-carbon alloys, they melt at 1500 ° C, and the ignition process occurs at 1300 o C.
For high-quality operation of the installation, it is necessary to provide a permanent supply of gas, since the oxygen requires a constant amount of heat, which is mainly maintained (by 70%) due to the combustion of the metal and only 30% provides a gas flame. If it is stopped, the metal will cease to produce heat and oxygen will not be able to perform functions assigned to it.
Work cutter, Metal cutting training
The maximum temperature of manual gas cutters reaches 1300 ° C, this is a sufficient value for the processing of most types of metal, however, there are those that begin to melt at highly high temperatures, for example, oxide aluminum - 2050 o C (it is almost three times more than the temperature melting pure aluminum), steel with chromium content - 2000 o C, nickel - 1985 o S.
If the metal is not enough and the melting process is not started, oxygen will not be able to oust refractory oxides. The inverse this situation, when the metal has a low melting point, under the influence of burning gas, it can simply melt, so it is impossible to use this method of cutting for cast iron.
Safety technique
Implementation of metal cutting using a gas installation is better to entrust the experienced specialist, since with inaccurate appeal the consequences can be sufficiently sad.
Safety involves the following conditions:
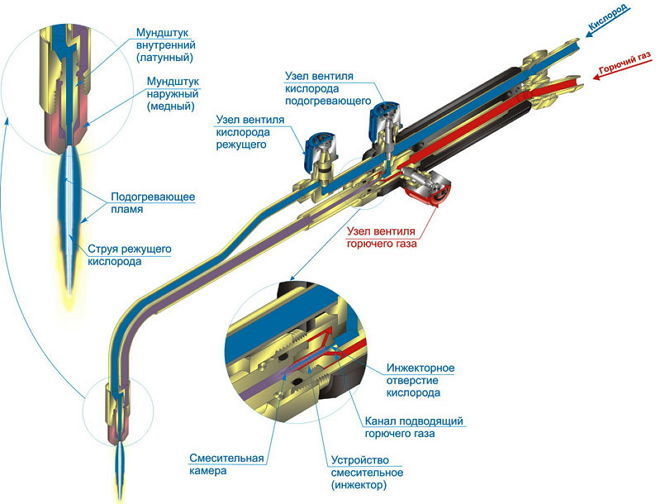
- good ventilation indoors where work will be carried out;
- at a distance of 5 meters there should be no cylinders with gas and other combustible substances;
- work should be carried out in a protective mask or special glasses, as well as in refractory clothing;
- direct the flame is necessary in the opposite direction from the gas source;
- the hoses in the process of operation of the device can not be launched, to occur on them, clamping their feet;
- if a break is done, then the flame at the burner should be fully replied to the burner and tighten the gas valves of cylinders.
Compliance with these simple conditions will ensure safe and efficient work on metal cutting gas installation.
Video: Work cutter, metal cutting training
